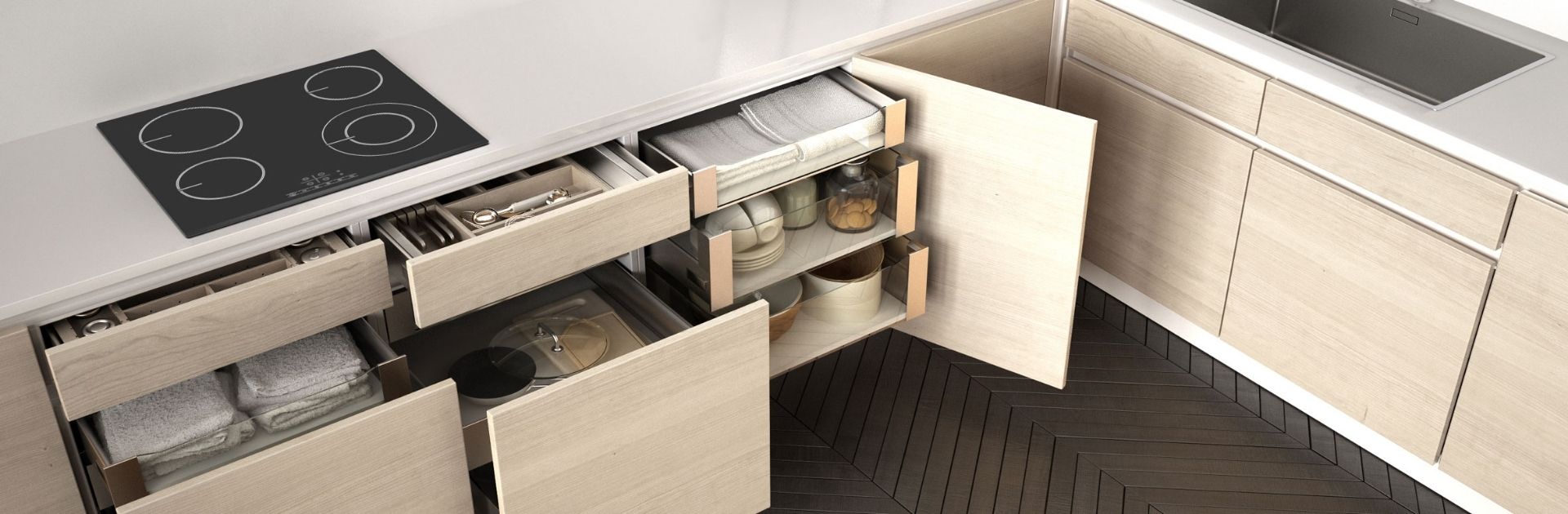
Nel 2004 Vito Rimoldi SpA è coinvolta da un'importante azienda italiana di accessori per i mobili nella realizzazione in grande serie di piccoli particolari cilindrici di gomma espansa, che dovranno essere montati su linee automatiche, all’interno di dispositivi che limitano la velocità in chiusura di porte e cassetti.
Il problema
La tecnologia della tranciatura, originariamente utilizzata per la realizzazione degli sponge, presenta alcuni limiti dovuti alla deformazione del materiale in lavorazione.
Sebbene questo difetto sia gradualmente limitato, è evidente che non potrà mai essere completamente risolto.
Inoltre, ancor più grave è la difficoltà di poter garantire nel tempo la costanza dimensionale del pezzo, con tolleranze di pochi decimi.
Nel 2007, Vito Rimoldi SpA entra in contatto con altre aziende di componentistica per l’arredamento a livello mondiale e diventa chiaro che la tranciatura non è adatta per tutte le tipologie di prodotti richieste dal mercato.
Occorre utilizzare una tecnologia differente.
La sfida
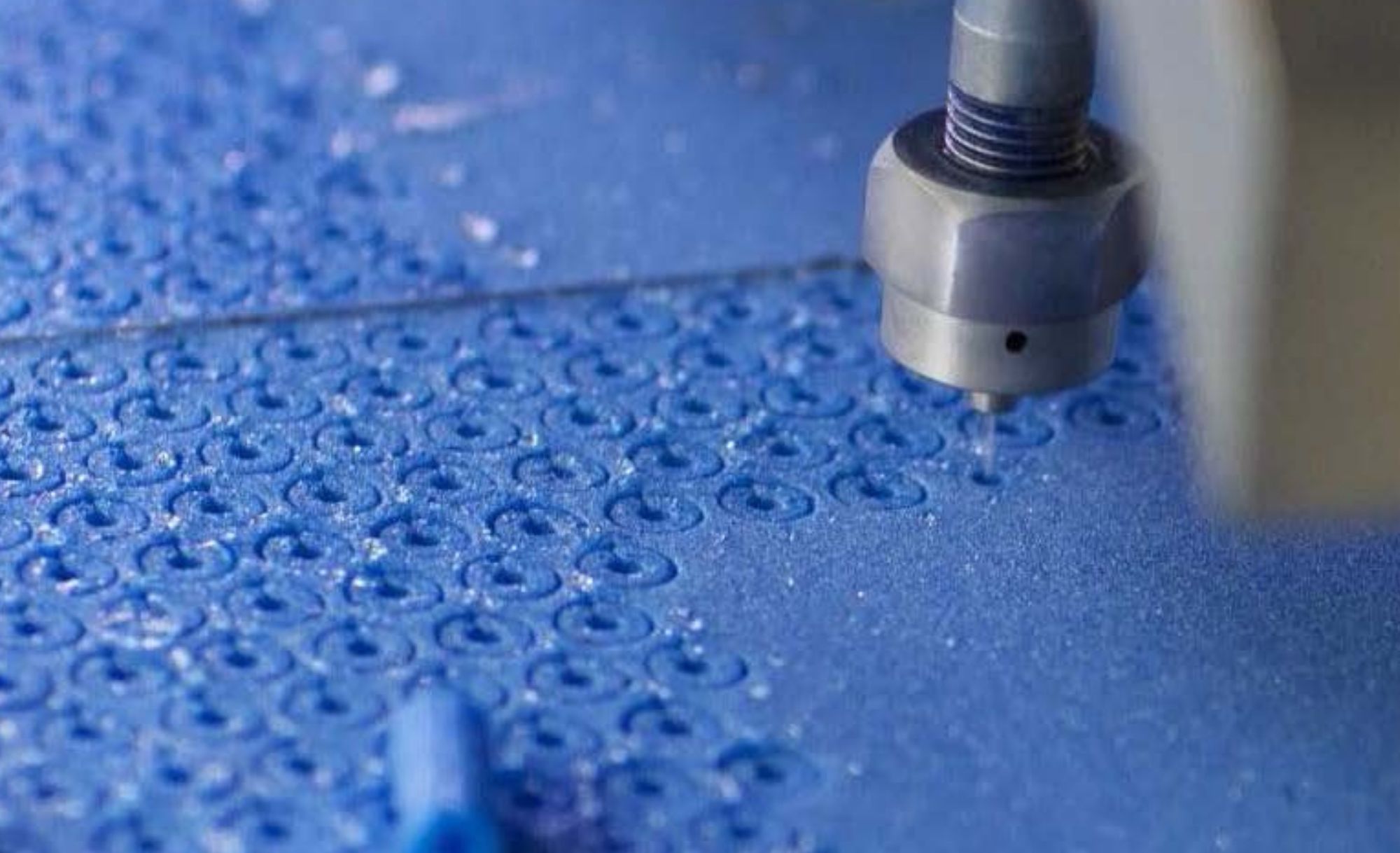
Ci si orienta sul taglio con getto d’acqua pura a pressione elevata, una tecnologia in cui Vito Rimoldi ha già una buona esperienza, perché da anni la utilizza per produzioni di piccole e medie quantità.
Tuttavia, le macchine water jet standard se da un lato hanno il pregio di essere molto versatili, dall’altro non hanno elevata produttività e si dimostrano poco adatte a produzioni di grandi serie come quelle che vogliamo affrontare noi.
La soluzione
L'azienda coinvolge un importante centro universitario italiano. Tra il 2007 e il 2008 si sviluppa una nuova macchina waterjet capace di garantire un livello di produttività adeguato al nostro obiettivo.
Si procede con una campagna di prove sperimentali (DOE), finalizzata alla definizione delle caratteristiche ottimali per gli ugelli di taglio e per tutti i parametri del processo del taglio ad acqua pura applicato a materiali spugnosi, e si sviluppa l’architettura di una nuova macchina di taglio, capace di governare più teste di taglio simultaneamente.
In base a quanto messo a punto, si realizzano i primi campioni per i primi Clienti esteri, raccogliendo valutazioni positive e l'incoraggiamento a proseguire con l’industrializzazione del processo.
Con il supporto di un costruttore specializzato in macchine customizzate, nel 2008, Vito Rimoldi SpA realizza la sua prima macchina di taglio specificamente destinata a questo tipo di produzione, con caratteristiche di precisione non reperibili sul mercato e una produttività adeguata a soddisfare le nuove esigenze.
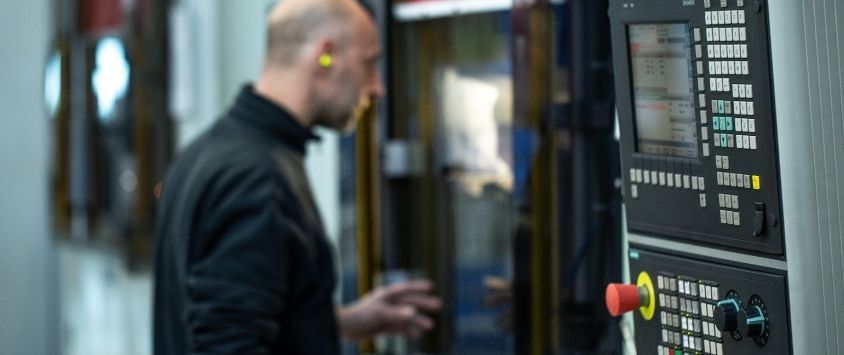
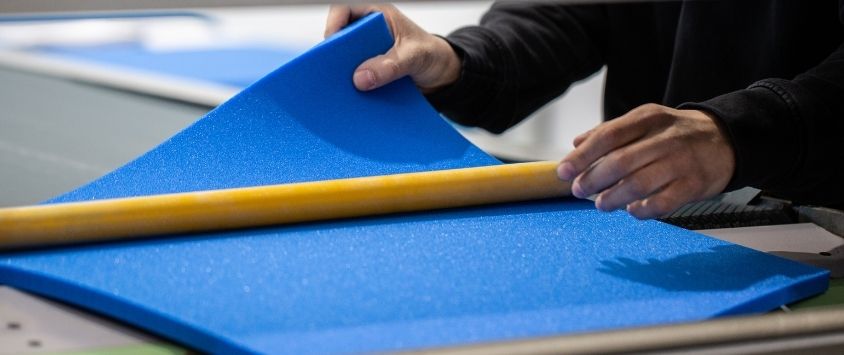
Un processo in miglioramento continuo
Macchinari per il controllo di grandi volumi produttivi
Nel 2008 partono le produzioni di 3 differenti Sponge Gaskets.
Sono particolari di piccole dimensioni e pesi molto ridotti perciò molto difficili da movimentare.
Nel 2009 Vito Rimoldi SpA coinvolge il Dipartimento di Meccanica del Politecnico di Milano per individuare la strumentazione e la metodologia adeguata a misurare, collaudare, selezionare e movimentare i pezzi.
L’anno successivo, con il supporto di un’azienda specializzata in linee di produzione automatizzate, si realizza la nostra prima stazione di controllo al 100% robotizzata a cui negli anni si affiancheranno macchine nuove e più performanti.
Macchinari per il taglio della materia prima
Poiché la percentuale di lastre scartate in accettazione è molto elevata e il fornitore non si dimostra capace di migliorare il proprio livello qualitativo, nel 2012 si decide di investire in una macchina a lama rotante per il taglio dei blocchi di spugna in lastre degli spessori desiderati.
A questo punto tutte le fasi del processo produttivo sono gestite internamente con notevole beneficio sulla qualità complessiva del prodotto finale.
Una strategia vincente
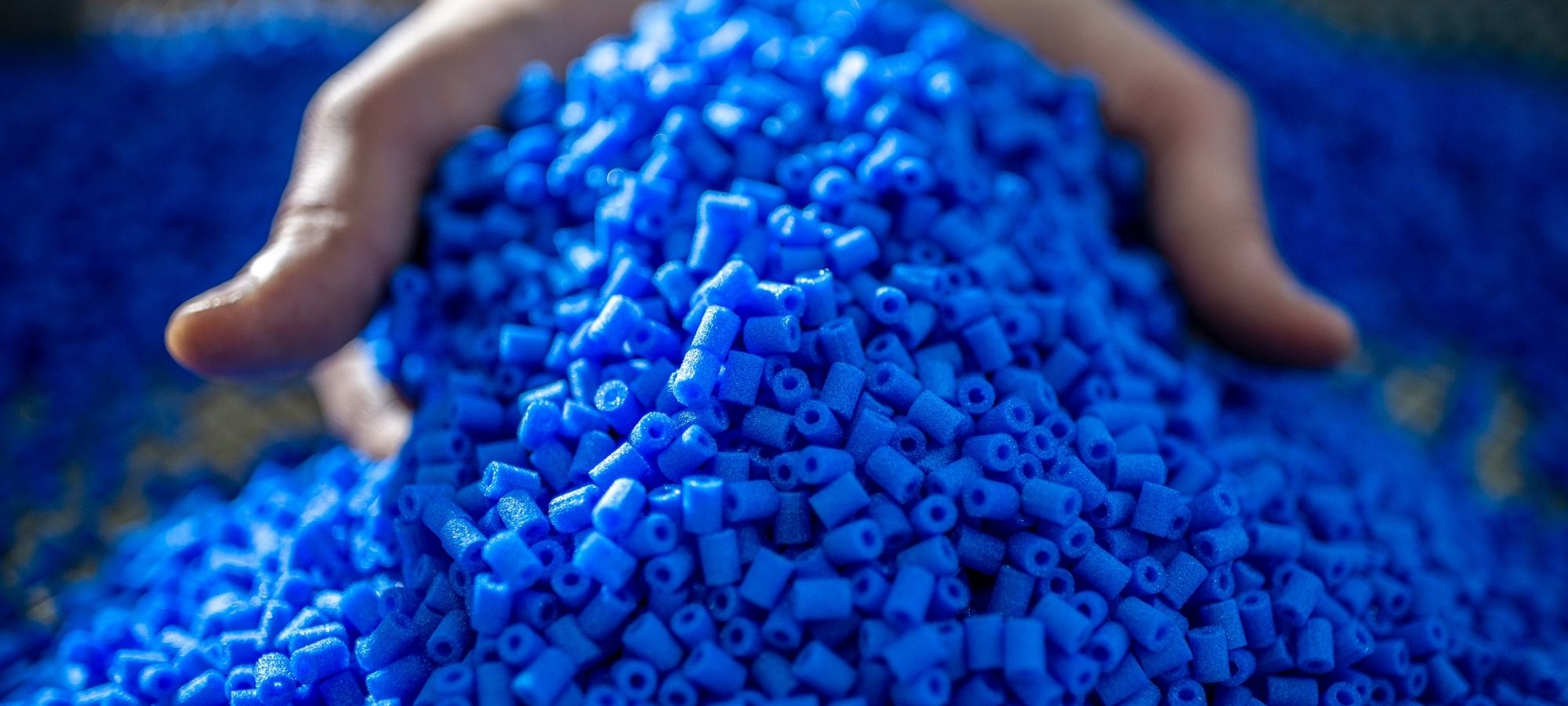
I continui investimenti per migliorare il prodotto e la capacità produttiva sono ricompensati dai nostri Clienti, confermando la strategia dell'azienda che si rivela vincente e vede crescere i volumi produttivi anno dopo anno.
Oggi il reparto produttivo degli Sponge Gaskets è in grado di realizzare diverse centinaia di milioni di pezzi l’anno, controllati al 100% e confezionati automaticamente.